許多車友來信詢問各式各樣的套件如何自己選購與安裝。
套件主要有下列幾種材質種類 :
* 【熱固、熱塑(GMT、SMC)製造的cFRP真碳纖維套件】
(歐洲約65~150萬)。
熱塑件要有強度,必須做5~6層攤纖+添加御禁布強化其產品結構。
此成型,多運用做為超跑等級車身輕量化骨架。
需開高碳鋼模製造。
是目前車業玩塑膠類算是超高檔的產品成型。
國內車業的經驗,有開發過的原廠件為Nissan X-Trail(T-30第一代)尾翼,便是在國內所製作。
----------------------------------------------------------
* 【PUR - 歐系車廠慣用高階軟質類橡膠材料】
缺點 :
產品單價高。
以FORD品牌在台售價最低,前+側+後4件套件,素材費約在6.8~8萬新台幣。
其餘VW、VOLVO、Land Rover、NMW等,一套4件通常素材費為12~30萬不等。
更高階品牌如麥拉倫,PUR套件通常素材費為60~80萬不等,再上去,就是上百萬的真碳纖為GMT、SMC(熱固、熱塑)成型套件。
模具應用範圍非常廣。
低階從樹脂模具-14層為標準製件,需加金屬、或強化纖維底座。
高階使用高碳鋼製作模具都有。
低溫模具,如果做低於14層又不做強化底座,就會跟亞太PU灌注手法一樣粗糙,成型就無法穩定,易變形、不良。
優點 :
耐熱高達500~700度。
如橡膠般耐擠壓。
表面有一層類似底塗+中塗層膠殼,通常為米白色,少數為灰底。
易於塗裝。
亞太地區目前沒有任何成型廠有能力做這樣耐熱高溫的PUR套件,完全沒有這種技術經驗。
原廠CX-5 MK1的前+後下護板,便是來自歐洲製造的PUR件。
@
目前公司在台灣本地製造,研製多年,材料尚不及歐洲製件耐高溫,耐熱溫度約80~100度之間。
其餘水準皆有達歐洲PUR套件標準,並符合國際亞太福特FLA認證測試。
----------------------------------------------------------
* 【PP - 射出成型】
ABS、PP、EPDM....等等多種類材質皆可。
高碳鋼模具製作精良,產品則會很穩定。
缺點 :
大陸、亞太地區通常為了降低射出高額的模具費,會使用次金屬材料製作模具,其成型素材表面便會很粗糙。
另外亞太地區也常打過多次料降低素材成本,便會造成素材表面難以塗裝。
塗裝時,需加以研磨加工後製處理,才能做好塗裝。
坊間賣很多雙B套件一組21000~33000的套件,大陸製國民車一組包素材從4000~15000之間都有,多數為次料做成的射出成型件。
素材毛邊就處理得不優,對塗裝來說,不一定會比做PU料素材好做到哪裡去。
如果以車廠高碳鋼精密加工製造。
混料次料為10%以內,則成品就很漂亮,質軟易研磨好上漆。
最大的缺點,仍然是模具成本過高,加上開高碳鋼成本大,製造模具前,更應該先製造1:1 Mork-up打樣加以確認成品實體是否有需調修。
如附圖 :
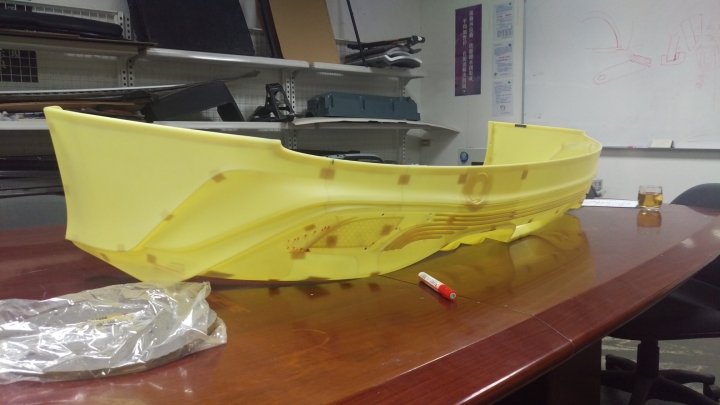
套件打樣成本相當昂貴,小包圍台灣打一套4件相當於45~50萬之間。
另外~
做到這個級數,如果像大陸射出的粗製濫造法,除了鋼模要省、材料打一堆次料,就也更不可能花上百萬做檢具+治具。
嚴格來說,做射出更應該要做檢具+治具,來確保產品的穩定性與檢驗方式控管產品。
但檢、治具其實也是非常昂貴的,開下去,百多萬肯定跑不了。
這便造就車廠做射出件成本攤提高的原因。
後話:
如果是開模用阿薩不入的搞下去,沒檢具、沒治具。
原則上,素材比亞太PU做更糟的都很常見。
但這類阿薩不入的素材,是目前在零售市場、掏寶、eBay普片常見的便宜質料。
大多為亞洲地區製造的配件。
優點 :
以正規射出開高碳鋼模+檢具+治具+台化新料做,品質是相當穩定的。
成型快速,為量產件最佳的生產法則。
----------------------------------------------------------
* 【ABS-真空熱吸塑成型】
目前亞太地區主流的空力套件成型方式。
開鋁模單面模具+抽氣孔,壓ABS板利用板材加熱吸塑成型+NC切割加工。
最大宗的製造成品,為行李箱、垃圾桶...類。
缺點 :
無法成型細膩的造型設計與複雜的機構。
畢竟它只是抽一張皮面起來。
遮噴溝、網格類...等等皆無法成型。
保桿、套件內側要長插枵是不可能的,只能靠後加裝另外組立替代,但後加裝這些物件,就必須訂做治具,一旦使用金屬治具,就沒有太大的效益,成本一旦過高,則建議開射出。
不耐輕微碰撞、擠壓,便會爆裂。
素材較無厚實感,較鬆垮。
優點 :
素材成品費低廉、易塗裝好著漆。
所以套件的價位通常在14500~18000之間,入手門檻相當低。
製造時間短,也是其優點之一。
是亞太地區,套件類少量幾百套生產與搭配廉價市場的最佳方式,難以被取代。
目前國內有這種成型套件原廠產品 :
Luxgen U6、Honda City....等等。
----------------------------------------------------------
* 【ABS-吹氣成型】
大多用來做尾翼、SUV前+後防碰撞桿類的套件。
需開中碳鋼模。
以吹氣成型。
缺點 :
大陸製的SUV前、後保桿吹氣防撞桿套件,最大的問題就是精密度非常差。
例如CR-V MK5的大陸製件,一組弄進台灣大約5500販售,組裝是靠自攻螺絲,從保桿正面攻牙進去,日後拆除,保桿是無法復原,得另外補洞+烤漆。
因為無法密合,所以會在貼面塞黑色海綿遮醜。
常看見公差達15~20mm都有。
塗裝也都做簡易型消光黑+銀霧,遮噴處理的很糟。
尾翼通常不論大陸、台灣,都是以拷貝原廠件為主。
取得的原件準,做出來就會準,取得的原件變形、孔位跑掉,貼面角度不對,就會跟著跑掉。
通常成型發現貼不到,就會補超過3mm以上的泡棉膠來補強,貼面的間隙就會超過3mm以上。
很多車友誤以為原廠尾翼也是這個成型方式做的,其實,絕大多數的原廠尾翼,都是射出變異PP件,並非吹氣。
模具+成本物料攤提,吹氣用不到射出的2~4成模具費。
優點 :
吹氣成型用中碳鋼模作業其實算是很成熟的製程。
尤其海上工具,很多是吹氣成型件,品質都有一定的水平,甚至比大陸的射出件還優。
台灣比較大的吹氣廠,例如台中晉惠,都是業界老廠。
但通常成型與模具廠是分開承接。
素材成品費勘比射出低廉,適合用來做上千件得準量產製程。
素材用ABS料,塗裝也更為省力,好施作。
----------------------------------------------------------
* 【PU - 亞太地區曾嘗試過做歐洲套件的兩翼型用料】
但多數在入門就放棄材料上的研發。
樹脂模具-膠殼約3~5層內,沒那個成本做太厚。sorry
缺點 :
軟料+油質嚴重的材料無法塗裝。
即使塗裝後,大約3~6個月即會產生漆面剝離,漆面塗裝作百格測試是肯定NG,因為是軟料,切割百格後套件稍微紐個角度,漆面就剝離了。
國內與大陸地區製造的PU件,多數沒技術做模內保壓、與規劃物料冷卻硬化的配方處理。
絕大多數,為低壓灌注,模內5~6分鐘左右即離模。
離模後又缺乏定型治具讓產品冷卻定型固化。
所以亞太地區的PU製造,不良品幾乎佔100%。
變型+無法塗裝成為亞太地區車業塑膠件難民。
優點 :
如歐洲PUR料皆為類橡膠軟料。
適應耐磨擦、擠壓。
----------------------------------------------------------
* 【FRP手積層 + cFRP真碳纖貼皮】+【FRP手積層】
產業內稱為假的真碳纖。
這是目前亞太地區最多人在製作的真碳纖維件積層作法。
本體是手積層FRP,表面貼碳纖布。
樹脂模具-膠殼約3~5層內,沒那個成本做太厚。XD
缺點 :
厚重,易從貼碳纖布底下的備膠產生包風、包水、膨脹、剝離的問題。
這類產品要做得好,完全取決於人工師傅做的慎密與否為主。
師傅心情好,FRP積層+cFRP碳纖維布貼面就會做得細心。
心情不好或趕工,包空氣就最常見。
車身件產品,大約6個月就會起泡龜、碳布浮起包風....等等奇奇怪怪的問題。
優點 :
好的手工,其實是工藝品,純客製化+限量本身就是需要代價的。
日本在手積層做套件,大概是全球知名的優異。
因為日本廠就是慢慢靠職人全心慢慢積層做起來。
一支前保桿,素材大約要做2週天,所以一支日製的積層FRP件保桿,通常都要5~6萬新台幣以上。
其他亞太地區,因為產品行情市價低,不可能會有業者,願意投資手積層在那邊給師傅戳氣泡,慢慢貼纖維布。
做個1~2層,就嫌麻煩嚕!
1天就要做好幾支前下巴,哪會去管裡面包風、含水....有的沒的。XD
材料大致為上述種類。
如附圖,套件完裝精美與否,會有所差異。安裝部分,下一篇會在分類書寫給大家參考。
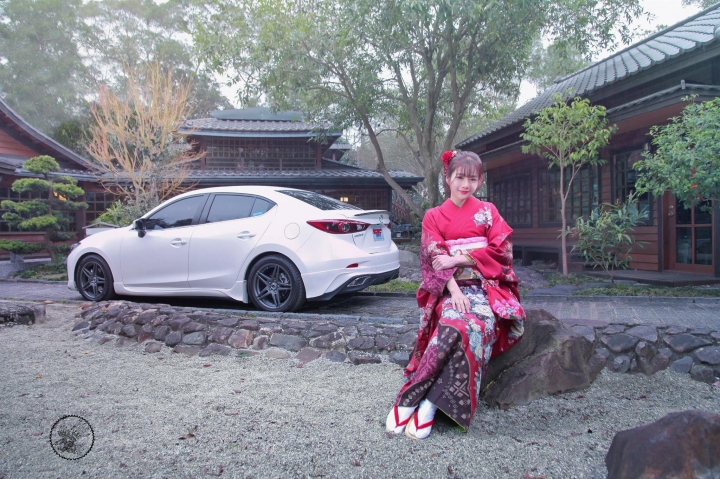
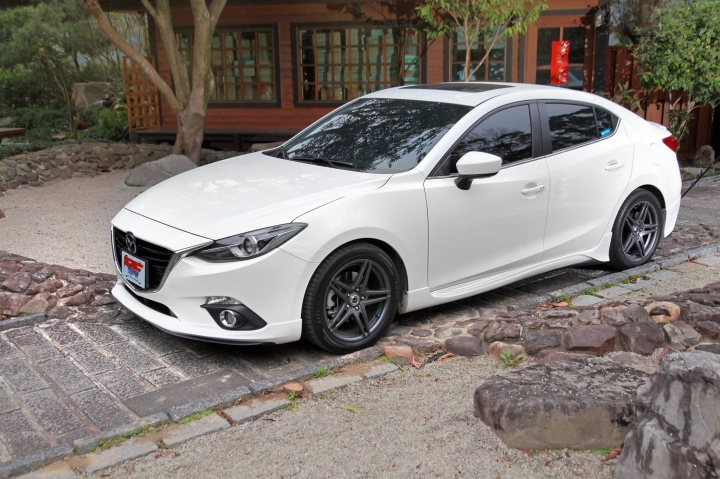
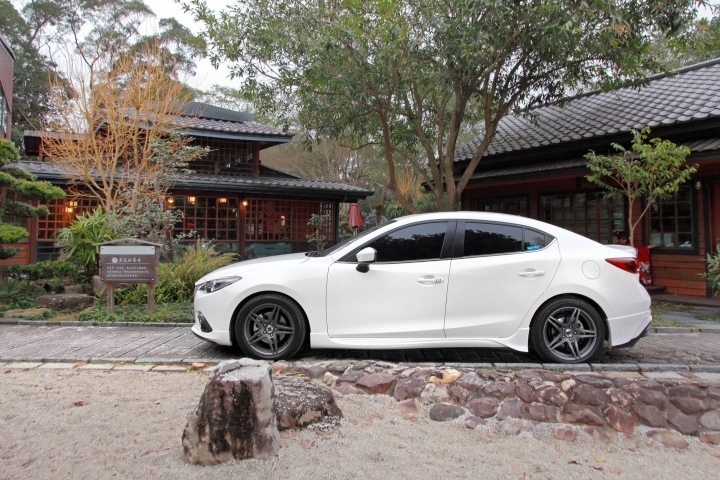
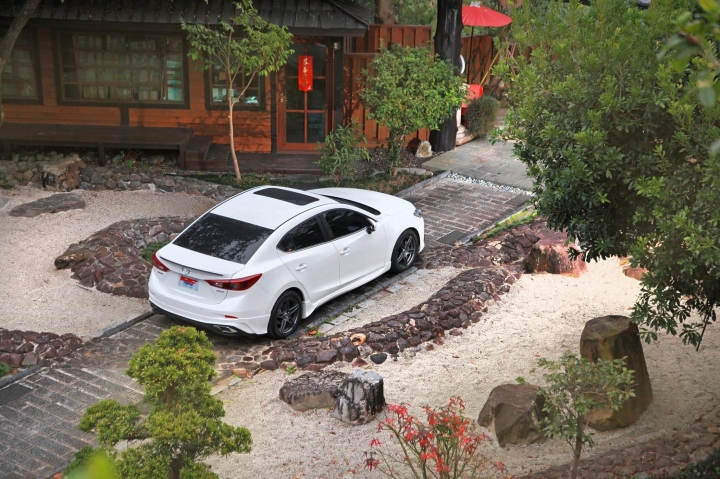
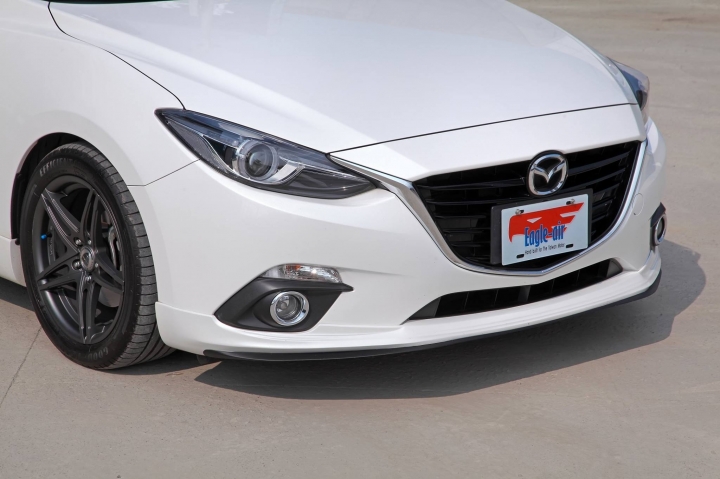
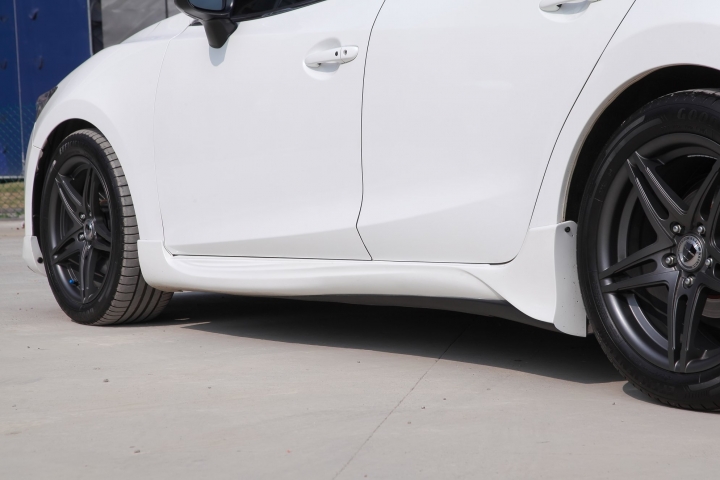
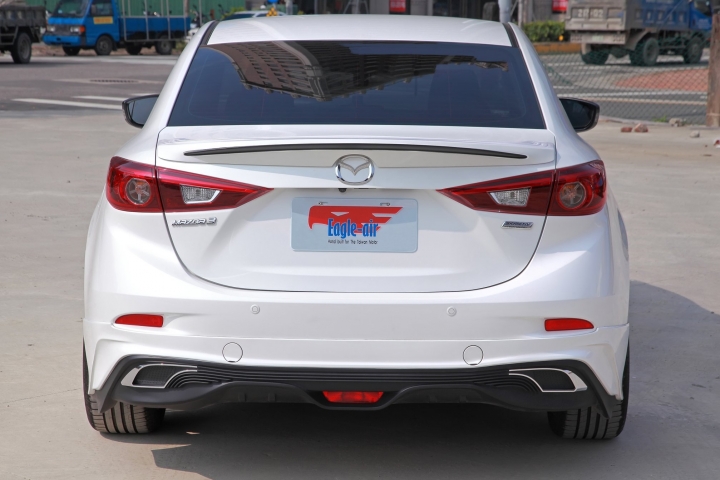
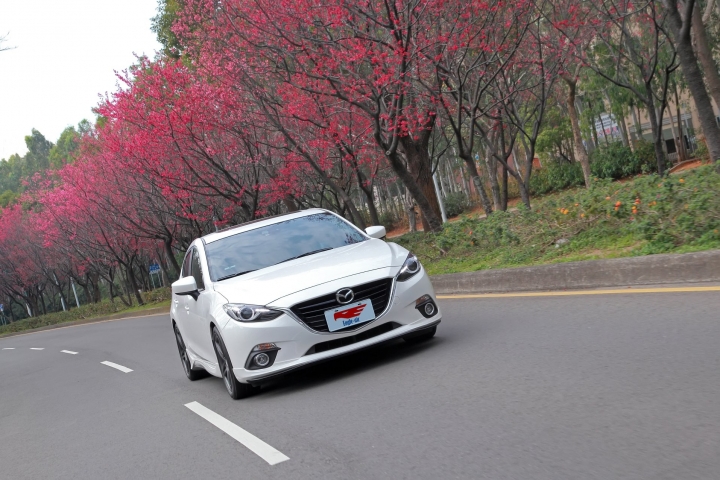
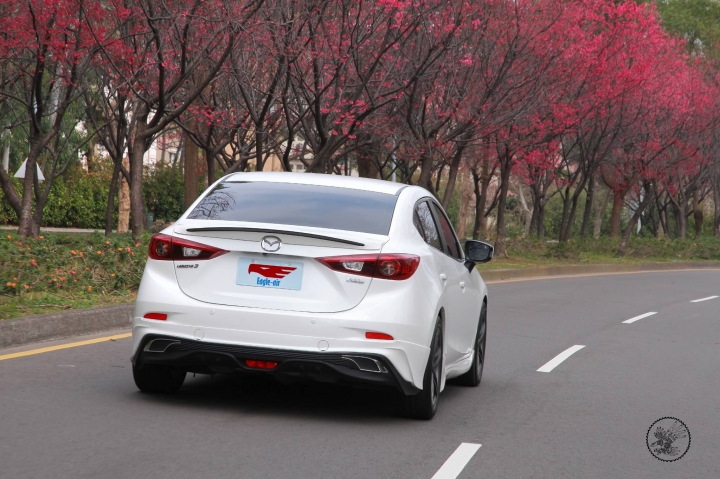
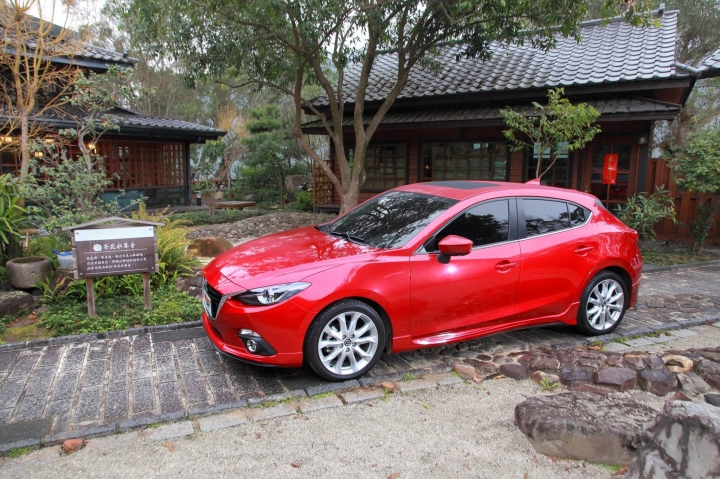
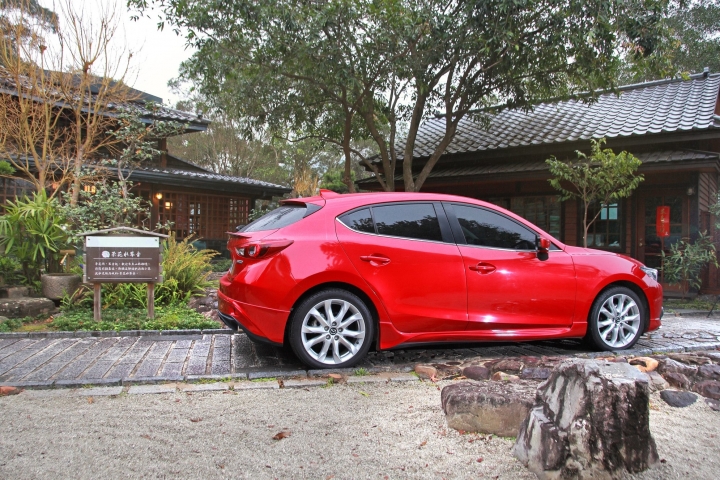
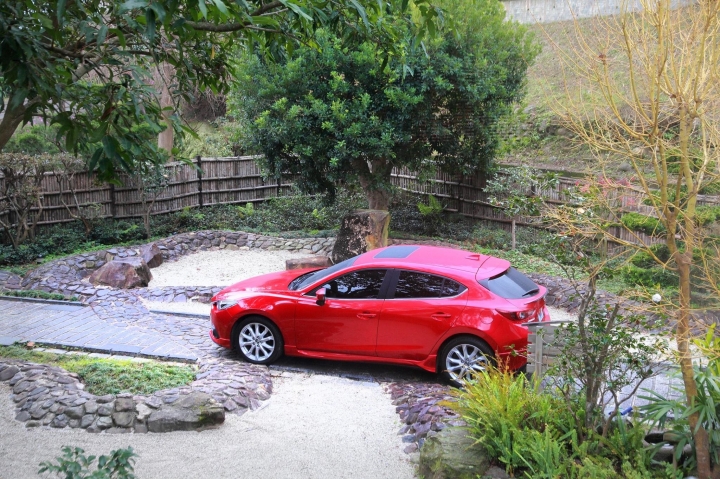
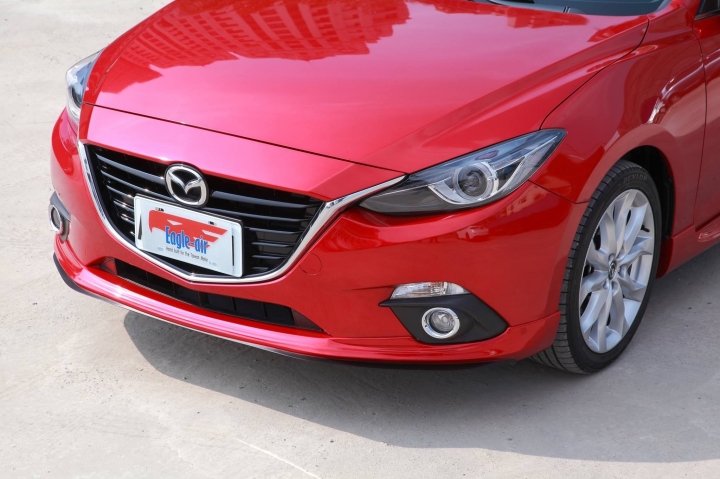
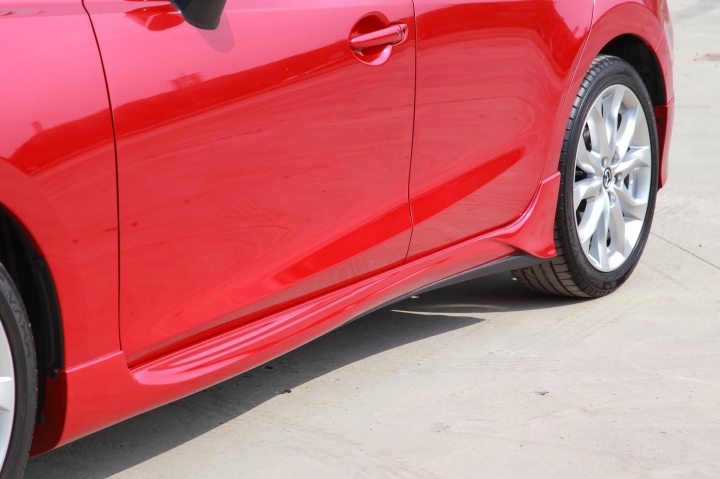
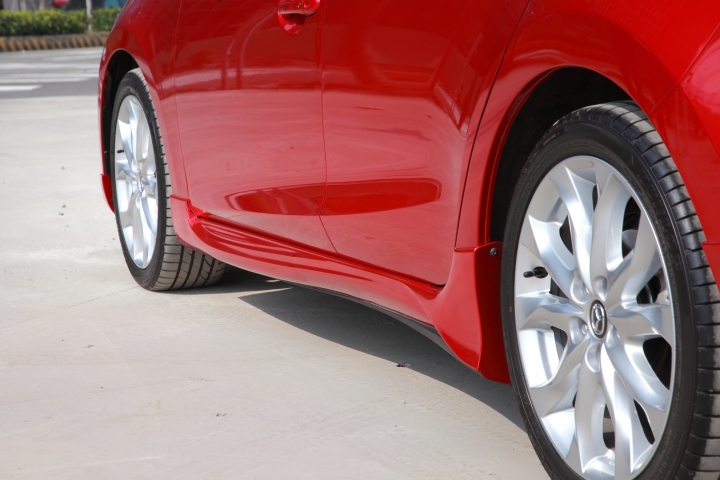
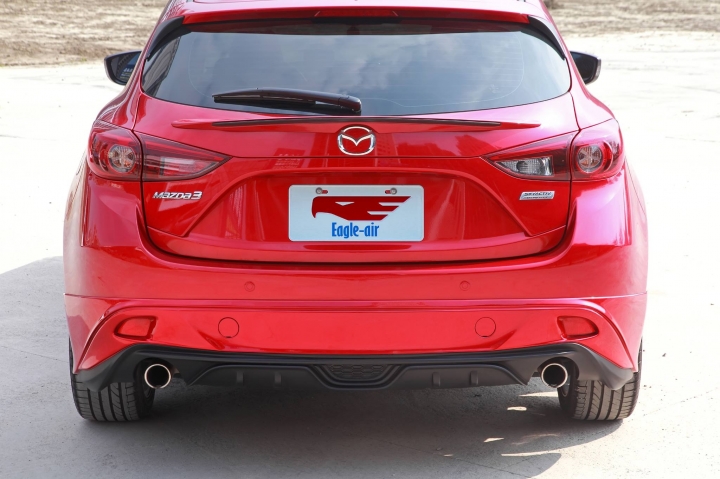
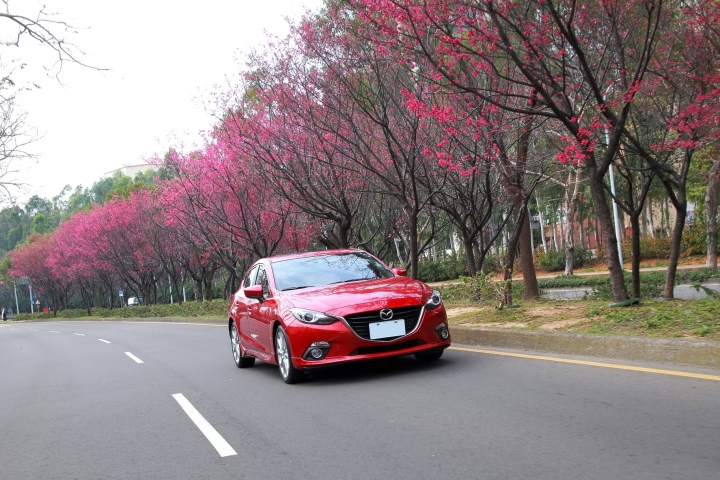
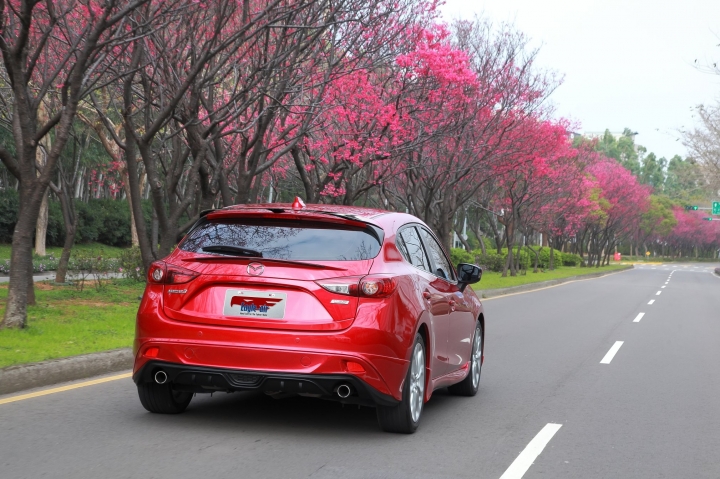
前下巴安裝圖例 :
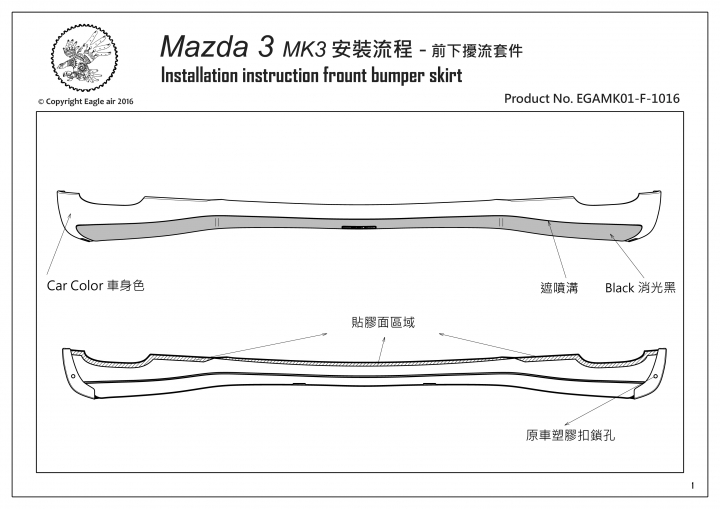
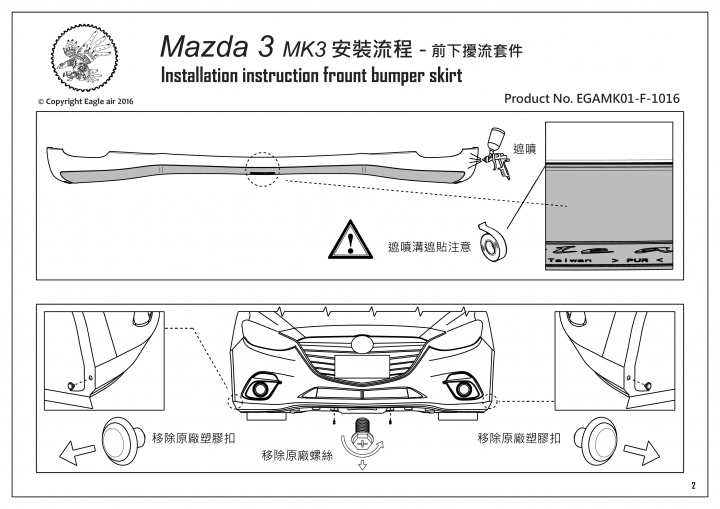
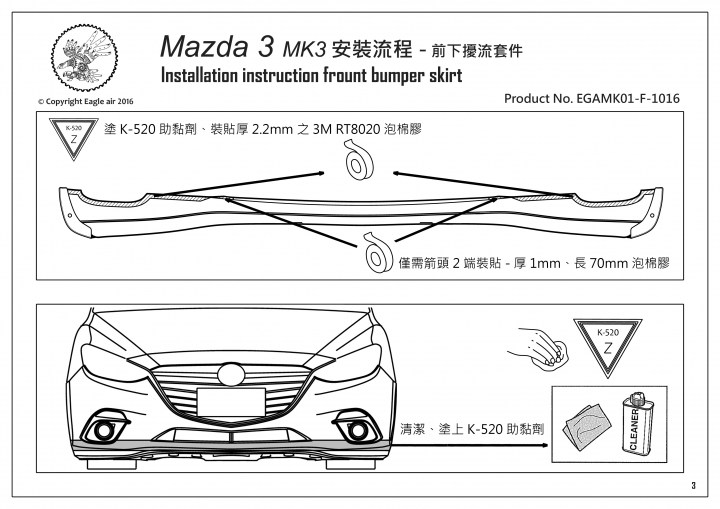
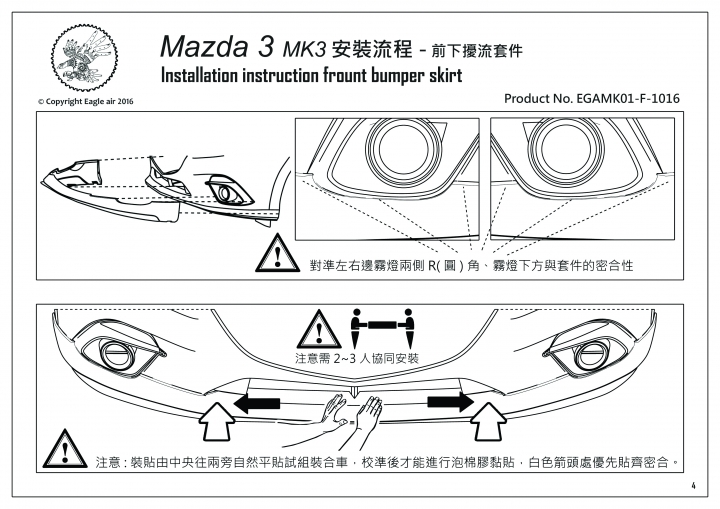
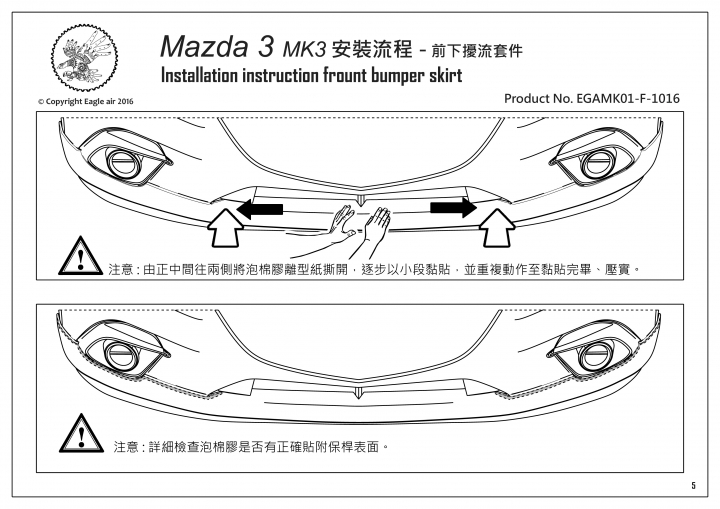
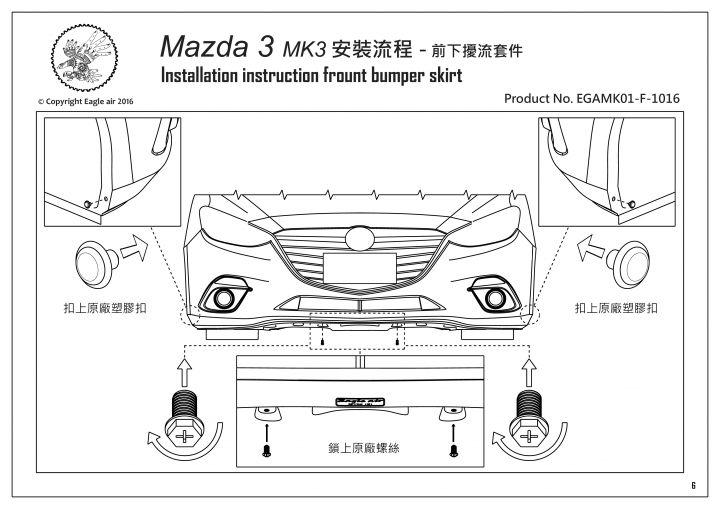
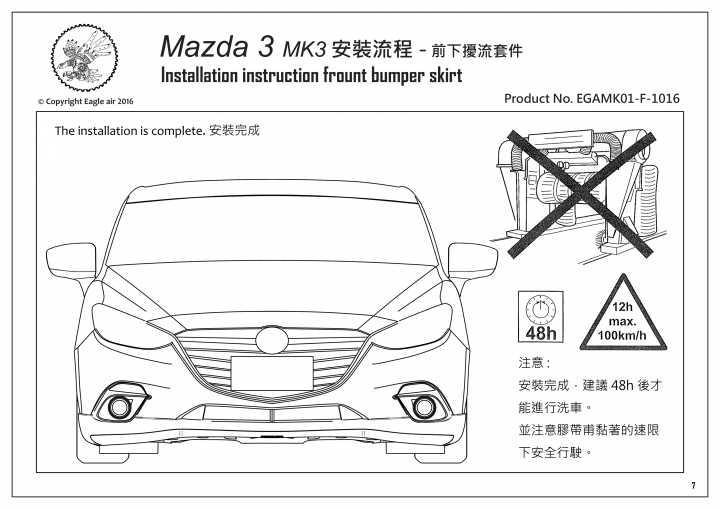
側裙安裝圖例 :
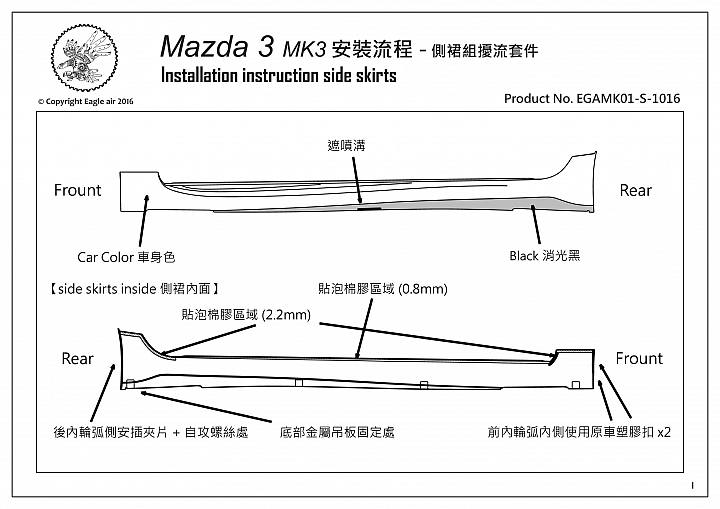
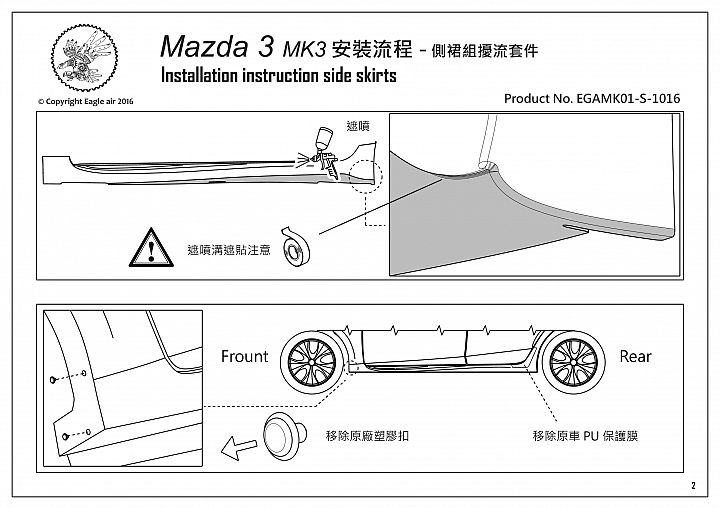
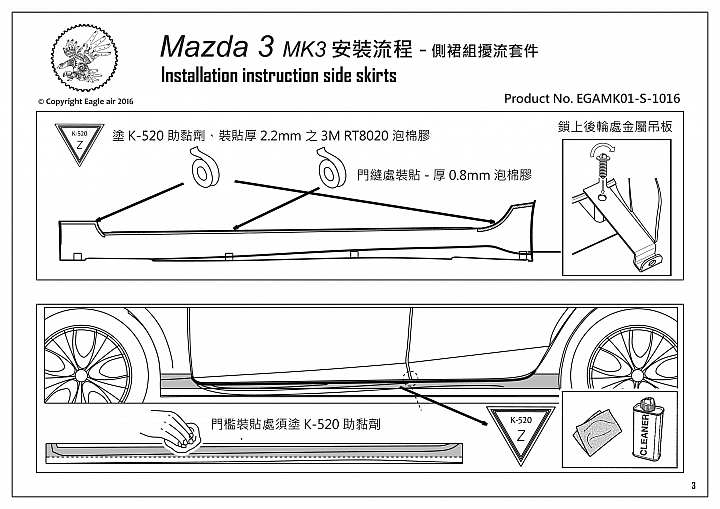
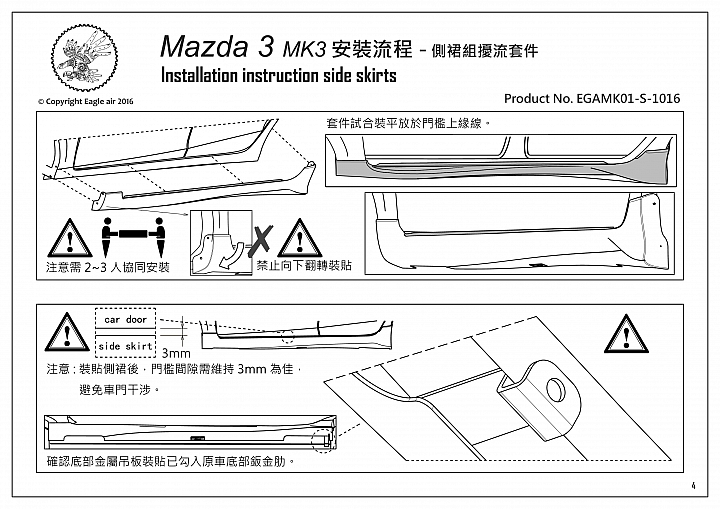
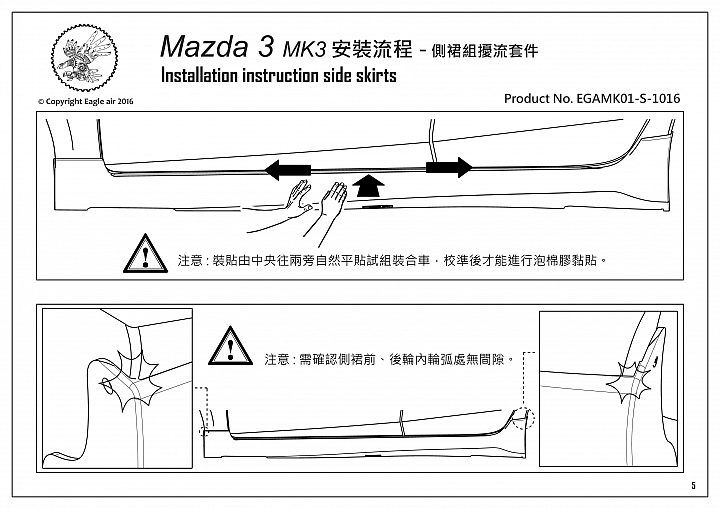
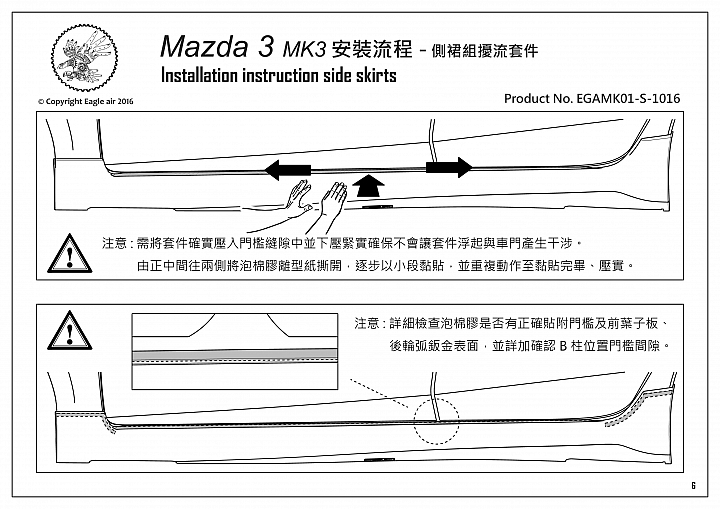
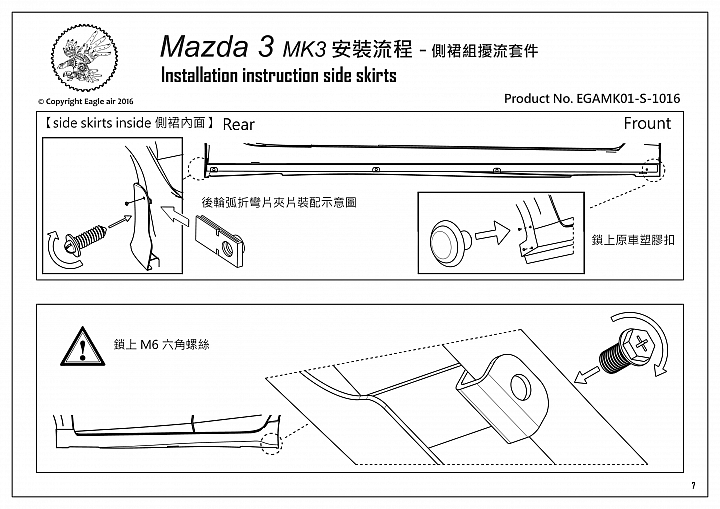
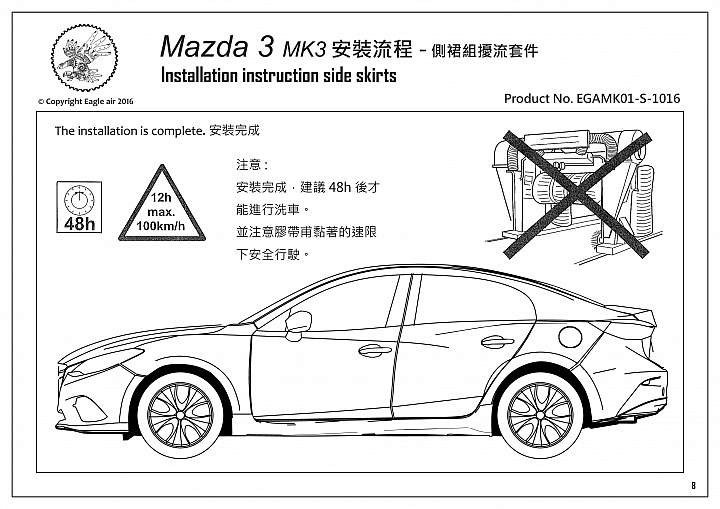
4D後下巴安裝圖例 :
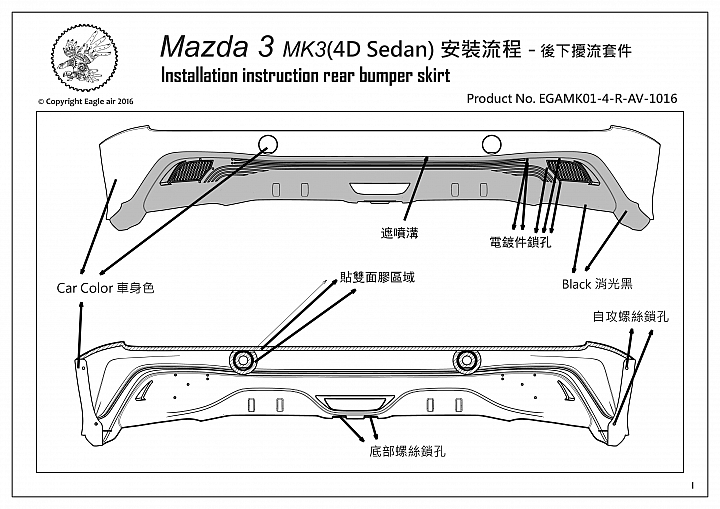
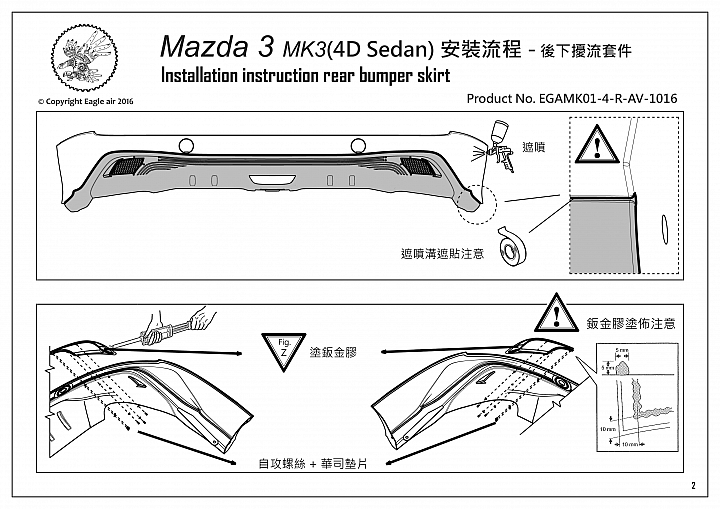
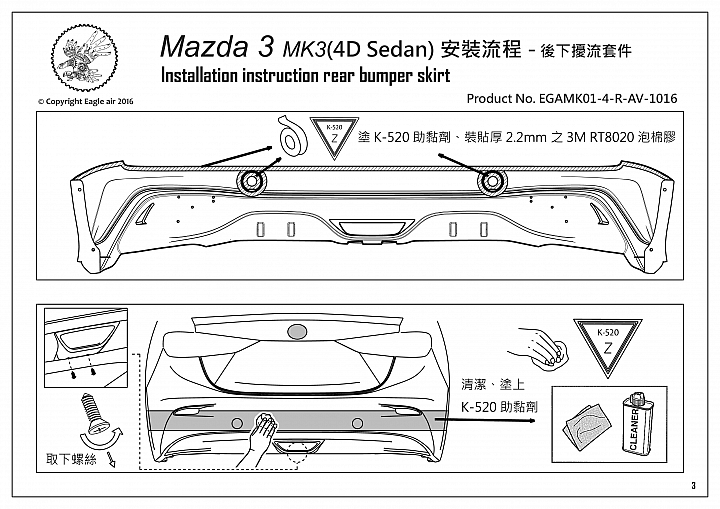
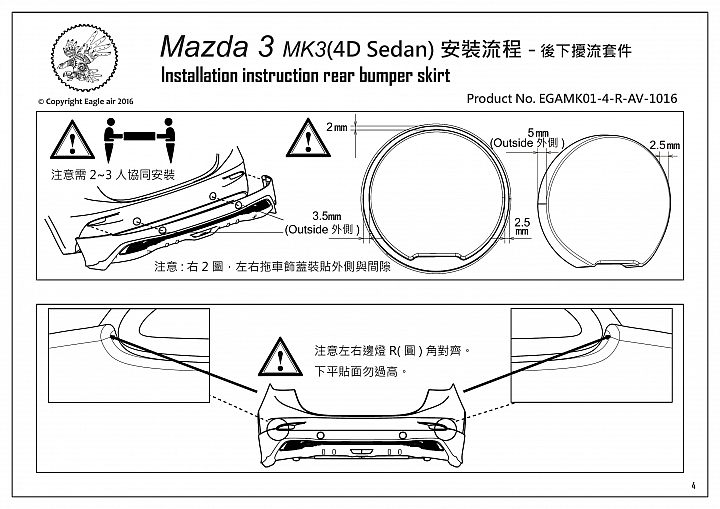
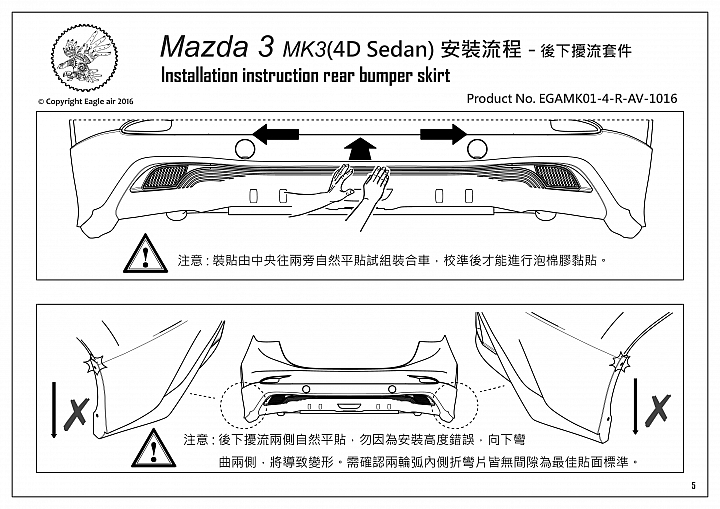
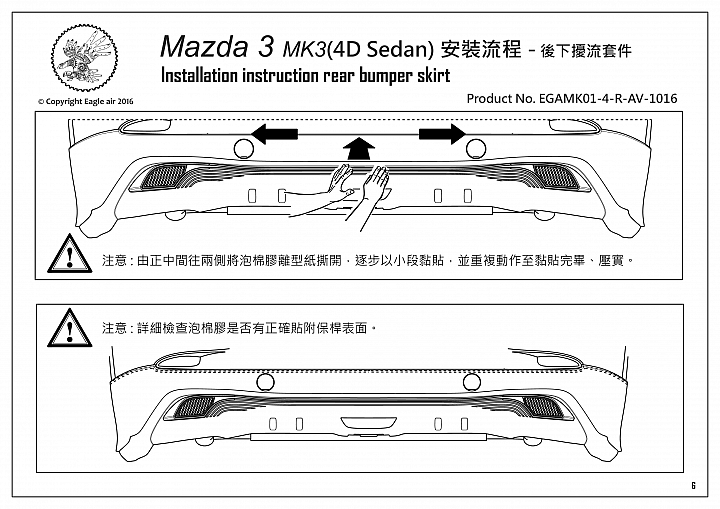
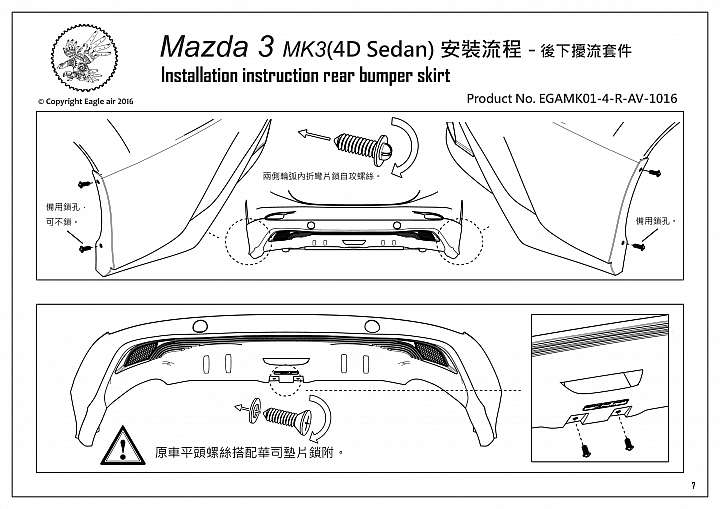
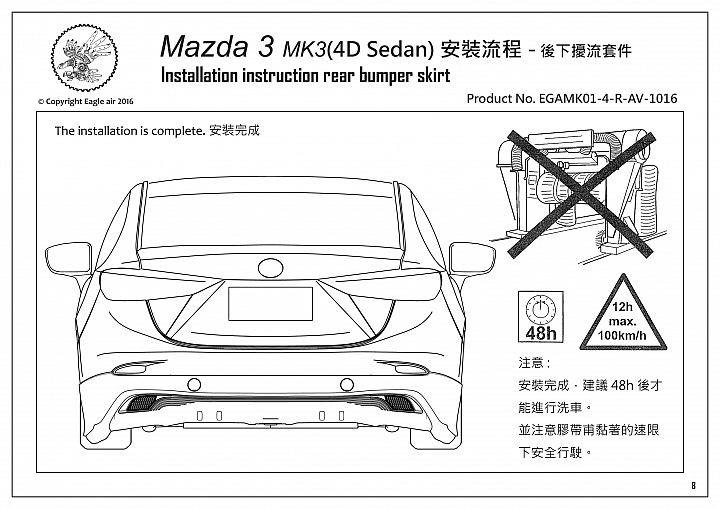
例如側裙在安裝上,就必須特別注意上面附圖,前輪弧處的塑膠扣孔位搭接,是否有作不當轉動角度,作不良貼附。
如下面附圖,不同的安裝施作手法,便會產生不同的結果。
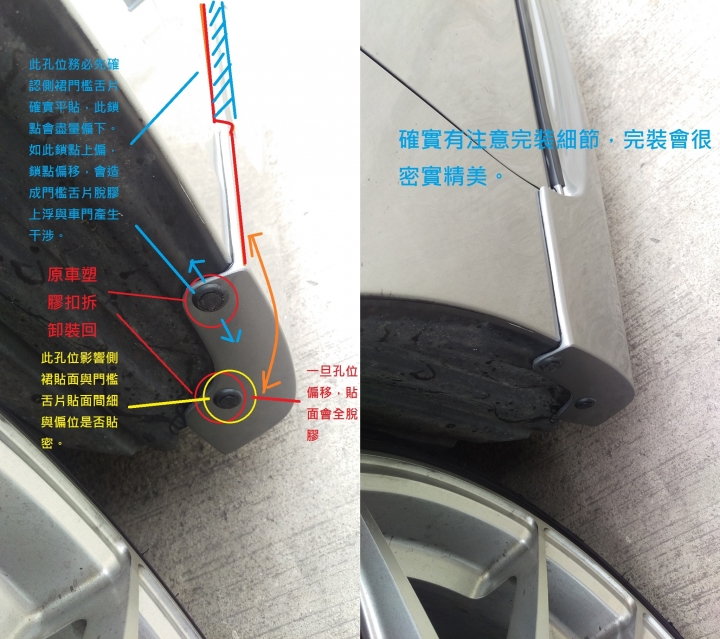
安裝組立,有許多眉角細節,大多是常被坊間改裝、保養廠安裝忽略的,進而產生組裝公差,變異等其他問題!
會再另外整理一篇跟大家分享。